Why plastic extrusion is the best choice for mass production
Why plastic extrusion is the best choice for mass production
Blog Article
Recognizing the Basics and Applications of Plastic Extrusion in Modern Production
In the world of modern-day production, the technique of plastic extrusion plays an important role. Untangling the principles of this procedure reveals the true adaptability and possibility of plastic extrusion.
The Fundamentals of Plastic Extrusion Process
While it may show up complicated, the principles of the plastic extrusion procedure are based on fairly simple concepts. It is a manufacturing process where plastic is thawed and afterwards formed right into a continual profile with a die. The raw plastic product, typically in the type of pellets, is fed right into an extruder. Inside the extruder, the plastic is subjected to heat and pressure, causing it to melt. The molten plastic is then required through a shaped opening, referred to as a die, to develop a long, continual item. The extruded item is cooled down and after that cut to the preferred size. The plastic extrusion procedure is thoroughly utilized in numerous industries as a result of its cost-effectiveness, adaptability, and performance.
Various Kinds of Plastic Extrusion Techniques
Building upon the fundamental understanding of the plastic extrusion procedure, it is required to discover the various strategies associated with this production method. Both primary methods are profile extrusion and sheet extrusion. In account extrusion, plastic is melted and developed right into a continuous account, frequently utilized to produce pipes, rods, rails, and window frameworks. On the other hand, sheet extrusion develops big, level sheets of plastic, which are commonly additional refined into products such as food packaging, shower curtains, and auto parts. Each method needs specialized equipment and specific control over temperature and pressure to guarantee the plastic preserves its form throughout air conditioning. Recognizing these techniques is essential to using plastic extrusion effectively in contemporary manufacturing.
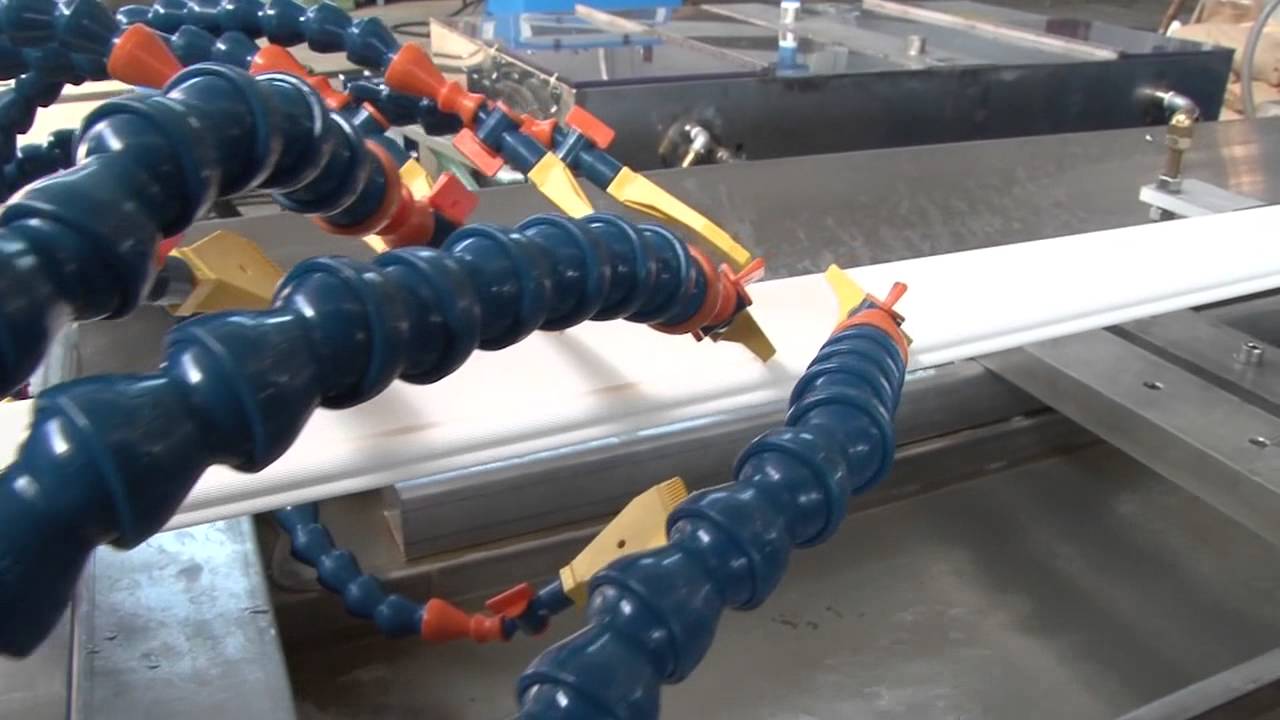
The Role of Plastic Extrusion in the Automotive Sector
A frustrating majority of parts in contemporary automobiles are items of the plastic extrusion procedure. Plastic extrusion is primarily utilized in the manufacturing of different automobile parts such as bumpers, grills, door panels, and dashboard trim. Thus, plastic extrusion plays an essential website link duty in automotive manufacturing.

Applications of Plastic Extrusion in Customer Product Production
Past its substantial effect on the auto industry, plastic extrusion shows similarly reliable in the world of customer items making. This process is crucial in developing a broad range of items, from food packaging to home home appliances, toys, and even medical gadgets. The flexibility of plastic extrusion allows manufacturers to develop and produce complex sizes and shapes with high accuracy and performance. Moreover, as a result of the recyclability of lots of plastics, squeezed out components can be reprocessed, lowering waste and price. The versatility, adaptability, and cost-effectiveness of plastic extrusion make it a preferred option for numerous consumer products producers, adding significantly to the sector's development and advancement. However, the ecological ramifications of this extensive use call for cautious consideration, a topic to be reviewed better in the subsequent section.
Environmental Influence and Sustainability in Plastic Extrusion
The pervasive usage of plastic extrusion in producing invites analysis of its ecological ramifications. As a procedure that frequently uses non-biodegradable products, the ecological her explanation influence can be significant. Energy consumption, waste production, and carbon exhausts are all worries. Industry innovations are raising sustainability. Effective machinery reduces energy use, while waste management systems recycle scrap plastic, lowering basic material needs. In addition, the growth of biodegradable plastics offers a more environmentally friendly choice. Despite these improvements, further development is needed to reduce the environmental footprint of plastic extrusion. As society leans towards sustainability, suppliers must adapt to remain viable, emphasizing the significance of continuous research and development in this field.
Conclusion
Finally, plastic extrusion plays a crucial function in modern manufacturing, especially in the auto and consumer items markets. Its flexibility permits the production of a large range of components with high accuracy. Its capacity for recycling and development special info of naturally degradable materials supplies a promising opportunity towards sustainable techniques, thus addressing environmental worries. Understanding the fundamentals of this process is vital to maximizing its applications and advantages.
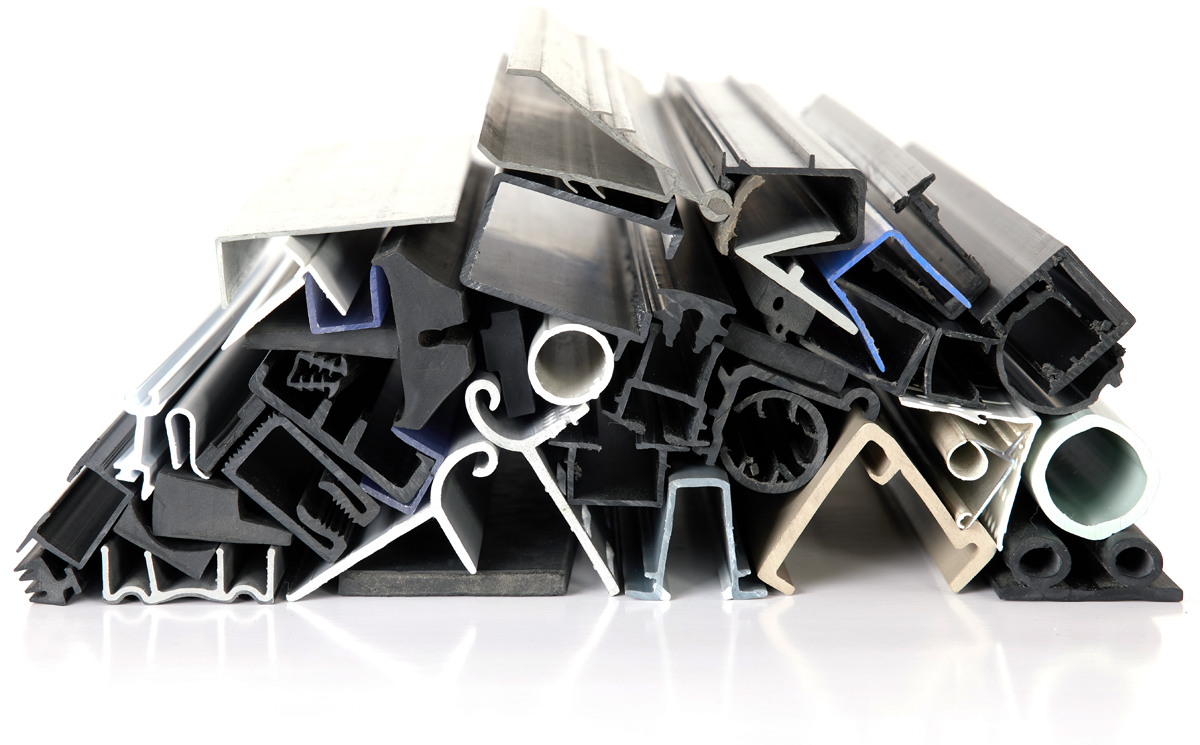
The plastic extrusion procedure is extensively used in various sectors due to its cost-effectiveness, efficiency, and versatility.
Structure upon the fundamental understanding of the plastic extrusion process, it is necessary to explore the numerous strategies included in this manufacturing approach. plastic extrusion. In comparison, sheet extrusion creates large, level sheets of plastic, which are generally more processed into products such as food packaging, shower curtains, and automobile parts.A frustrating majority of parts in modern-day automobiles are items of the plastic extrusion process
Report this page